Troubleshooting Common Issues with Bottle Labeling Adhesives
- luisperalta7
- Sep 29, 2023
- 4 min read
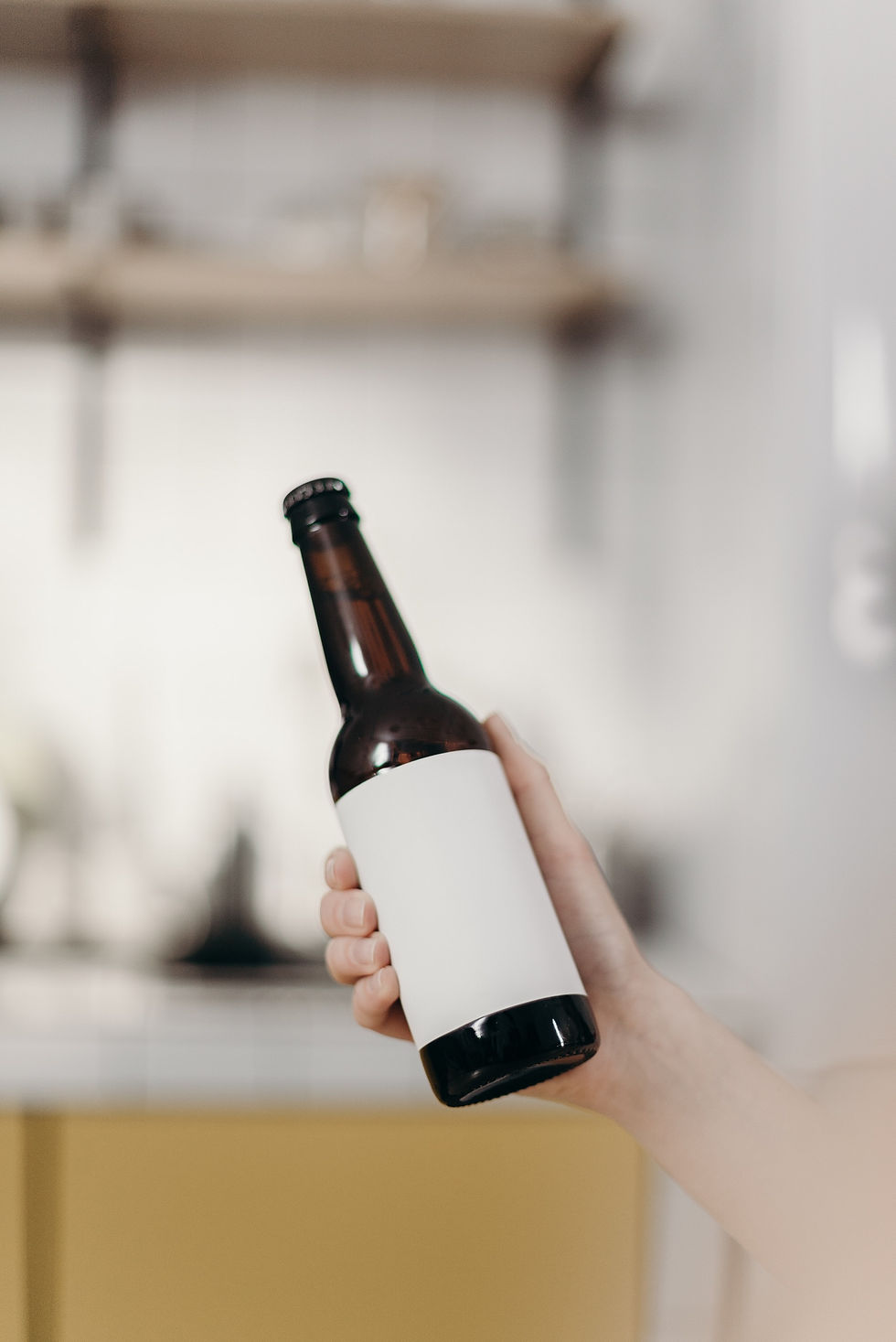
Are you tired of dealing with bottle labeling issues that never seem to go away? Whether it's labels peeling off, wrinkling, or shifting during shipping, these common problems can be frustrating and costly for your business. But fear not, because in this article, we will troubleshoot these issues and show you how to overcome them.
When it comes to bottle labeling, the adhesive used plays a crucial role.
It needs to be strong enough to withstand different environmental conditions, yet flexible enough to conform to the shape of the bottle. In this brand voice, we understand the importance of finding a balance between strength and flexibility to ensure a reliable and visually appealing label.
Throughout this article, we will dive deep into the most common bottle labeling adhesive problems and provide practical solutions to overcome them. From understanding the root causes to implementing practical troubleshooting techniques, we'll cover everything you need to know to fix bottle labeling issues and ensure smooth production.
So, if you're ready to put an end to your bottle labeling headaches and improve the overall efficiency of your production line, keep reading. We have the answers you've been looking for.
Common issues with bottle labeling adhesives
Problem: Labels not sticking properly
One of the most frustrating issues with bottle labeling is when the labels simply don't stick properly. This can result in a messy appearance, as well as potential damage to your product's branding and information. Fortunately, there are several steps you can take to ensure your labels stick securely to the bottle.
First and foremost, it's crucial to choose the right adhesive for the bottle material. Different materials have different surface properties, so it's essential to use an adhesive that is specifically designed for the material you're working with. For example, if you're labeling glass bottles, a high-tack adhesive is recommended to ensure a strong bond. On the other hand, plastic bottles may require an adhesive with more flexibility to accommodate their shape.
In addition to selecting the right adhesive, proper label application techniques are also essential. Make sure the surface of the bottle is clean and free from any dust, oil, or residue. This can be achieved by using a mild detergent and water solution to wipe down the bottle before applying the label. Additionally, ensure that the label is applied smoothly and evenly, without any wrinkles or bubbles. Using a label applicator or dispenser can help achieve a consistent and professional-looking result.
By following these steps and choosing the right adhesive for your bottle material, you can ensure that your labels stick securely and provide a visually appealing finish.
Problem: Labels peeling off over time
Another common issue with bottle labeling adhesives is labels peeling off over time. This can be particularly problematic if your products have a long shelf life or if they are exposed to varying environmental conditions. Fortunately, there are measures you can take to prevent labels from peeling off and maintain the integrity of your branding and product information.
Firstly, it's important to consider the adhesive's long-term durability. Look for adhesives that are specifically designed for long-lasting performance and can withstand exposure to moisture, heat, and cold temperatures. UV-resistant and water-resistant adhesives are particularly effective in preventing labels from fading or smearing.
Proper label application is also crucial in preventing labels from peeling off. Ensure that the surface of the bottle is clean and dry before applying the label. Avoid applying labels to bottles that are too cold or too hot, as extreme temperatures can affect the adhesive's performance.
By selecting adhesives with long-term durability like AQUENCE XP 7010T and implementing proper label application techniques, you can minimize the risk of labels peeling off over time and maintain the professionalism of your products.
Problem: Labels wrinkling or bubbling
Wrinkling or bubbling of labels is another frustrating issue that can occur during the bottle labeling process. Not only does it impact the overall appearance of your products, but it can also compromise the readability of important information. Fortunately, there are steps you can take to prevent labels from wrinkling or bubbling and ensure a smooth and professional finish.
One of the main causes of wrinkling or bubbling is improper management of temperature and humidity during the labeling process. It's essential to ensure that the environment in which the labeling takes place is within the recommended temperature and humidity range. Extreme temperatures or high humidity levels can cause the adhesive to become too tacky or too dry, resulting in poor adhesion and wrinkling or bubbling of the labels.
To prevent this issue, consider investing in temperature and humidity control equipment for your labeling area. This will help maintain a consistent and optimal environment for labeling. Additionally, allow sufficient time for the labeled bottles to acclimate to the ambient temperature and humidity before packaging or shipping. This will allow the adhesive to fully bond with the bottle surface, reducing the risk of wrinkling or bubbling.
Furthermore, selecting adhesives that are specifically designed to resist wrinkling or bubbling can also be beneficial. These adhesives often have a higher degree of flexibility and can better accommodate the expansion and contraction of the bottle material due to temperature changes.
By managing temperature and humidity, allowing sufficient acclimation time, and using adhesives that resist wrinkling or bubbling, you can achieve a smooth and professional finish for your labeled bottles.
Conclusion
Bottle labeling issues can be frustrating and costly, but with the right troubleshooting techniques, they can be overcome. By choosing the right adhesive for the bottle material, ensuring proper label application techniques, managing temperature and humidity, and using UV-resistant and water-resistant adhesives, you can eliminate common bottle labeling problems and ensure a smooth and efficient production process.
Don't let bottle labeling issues hold you back. Take the necessary steps to troubleshoot and address these problems, and you'll be on your way to achieving reliable and visually appealing bottle labels that enhance your brand image and customer satisfaction. Remember, a well-executed bottle label not only provides essential information but also serves as a powerful marketing tool—making a positive and lasting impression on your customers.
Comments